能源和材料效率是汽車設(shè)計(jì)師對面向未來的車型系列和經(jīng)濟(jì)上合理的解決方案的優(yōu)先考慮清單上的關(guān)鍵要求。該主題領(lǐng)域的范圍很廣。這包括由于更嚴(yán)格的車隊(duì)限制而產(chǎn)生的精簡的二氧化碳足跡,智能地使用材料和使用新型材料混合的可持續(xù)輕量化。雖然傳統(tǒng)的內(nèi)燃機(jī)汽車的重量較輕,可以減少破壞氣候的溫室氣體的排放,但更輕的電動汽車可以獲得額外的續(xù)航能力。
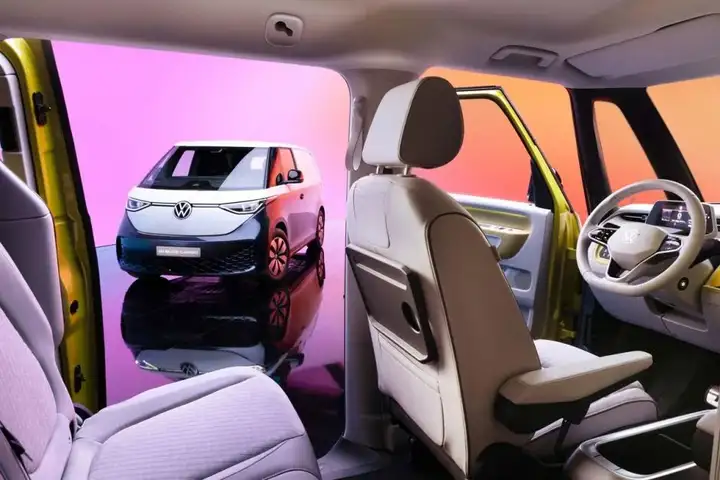
考慮到整體重量的雄心勃勃的車輛概念使用創(chuàng)新材料和不同材料的系統(tǒng)組合以形成功能性材料組合。然而,沒有靈丹妙藥。
新設(shè)計(jì)的電動汽車領(lǐng)域的標(biāo)志,緊湊型小型汽車BMW i3,在推向市場不長時(shí)間之后就已經(jīng)被制造商逐步淘汰。事實(shí)證明,由碳纖維增強(qiáng)塑料制成的乘客艙是一個(gè)成本驅(qū)動因素,而這款電動車先鋒的銷售數(shù)字遠(yuǎn)遠(yuǎn)低于預(yù)期。根據(jù)寶馬公司的說法,九年銷售中積累的損失加起來約為20億歐元,從而使得寶馬的碳核心多材料戰(zhàn)略受到了挫折。i3可能將由配備電動馬達(dá)的X1跨界車型繼承。
寶馬集團(tuán)也絕沒有停止其在輕量化領(lǐng)域的活動,并正在擴(kuò)大其在由天然材料制成的可持續(xù)的、節(jié)約資源的汽車部件領(lǐng)域的承諾。通過其風(fēng)險(xiǎn)投資部門BMW i Ventures,這家慕尼黑汽車制造商最近投資了瑞士公司Bcomp,一家由天然纖維制成的高性能復(fù)合材料制造商。
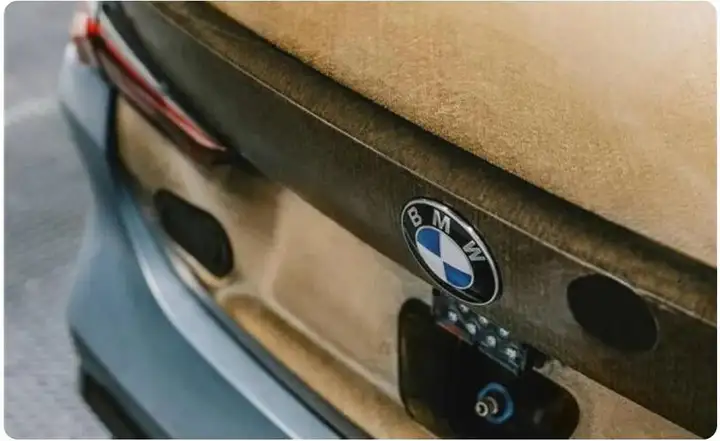
無獨(dú)有偶,沃爾沃也通過其風(fēng)險(xiǎn)投資子公司沃爾沃汽車技術(shù)基金(Volvo Cars Tech Fund)對瑞士Bcomp公司進(jìn)行戰(zhàn)略投資。
與傳統(tǒng)材料相比,采用可再生原材料和天然纖維,如亞麻、紅麻等,能最大限度減少材料的使用量,更可減輕多達(dá)50%的重量,這將有助于降低車輛在使用過程中的能源消耗。此外,使用天然纖維還能減少二氧化碳計(jì)算值,因?yàn)橹参镌谏L階段吸收二氧化碳釋放氧氣。

輕量化的新色調(diào)
昂貴的輕量化愿景是一回事,更具有可持續(xù)的材料和資源節(jié)約型制造工藝則是另一回事。汽車行業(yè)對廉價(jià)耐用的輕量化組件的呼聲越來越高,針對這種需求的努力已經(jīng)結(jié)出碩果。
例如,由于需求增加,塑料集團(tuán)和汽車供應(yīng)商科思創(chuàng)正在擴(kuò)大其聚碳酸酯復(fù)合生產(chǎn)線。這種合成生產(chǎn)的材料可以抵抗外部影響,不會分裂,還可以加工成大面積的組件。它的生產(chǎn)最近也考慮到了回收的原材料。
生產(chǎn)汽車天窗的專業(yè)公司偉巴斯特在其產(chǎn)品系列中推出了聚碳酸酯汽車天窗,與傳統(tǒng)的鋼制板條天窗,其重量可減輕3.5千克。
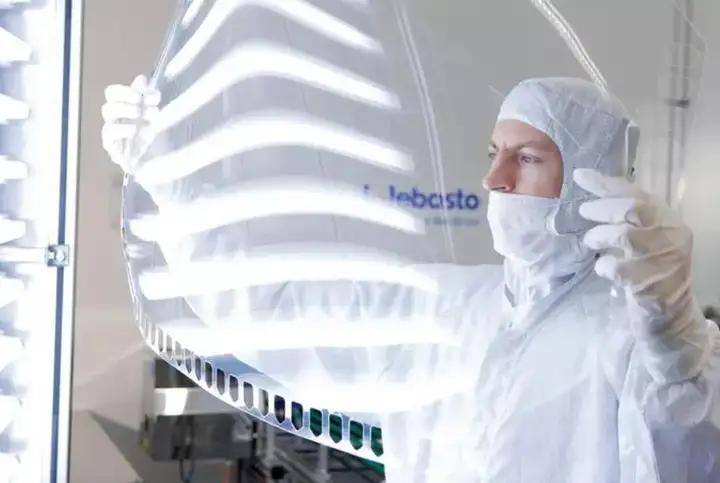
在車輛制造中,工業(yè)原材料的回收經(jīng)驗(yàn)參差不齊,但是,封閉的材料循環(huán)是纖維基復(fù)合材料的例外。一方面,復(fù)合材料的樹脂或塑料基體中的纖維無法在不損壞的情況下進(jìn)行回收,從而改變材料性能;另一方面,單一品種塑料的回收需要化學(xué)處理。這聽起來像是努力和額外的成本。然而,再生纖維和原材料減少了與組件相關(guān)的二氧化碳排放量。

降低成本的關(guān)鍵
以塑料為基礎(chǔ)的電池外殼蓋顯示了一個(gè)擺脫兩難困境的方法。來自德國宇航中心(DLR)的研究實(shí)驗(yàn)室展示了一個(gè)由玻璃纖維無紡布組成電動汽車的原型。
DLR的科學(xué)家們使用了熱塑性尼龍的基體和玻璃纖維非織造布。然而,仍然需要進(jìn)行優(yōu)化,以實(shí)現(xiàn)量產(chǎn)。材料和工藝成本的關(guān)鍵在于制造過程:為了使回收的無紡布達(dá)到穩(wěn)定的高質(zhì)量,工廠技術(shù)必須配備適當(dāng)?shù)膫鞲衅骱涂刂栖浖8鶕?jù)DLR的研究結(jié)果,與傳統(tǒng)的鋁制構(gòu)造相比,額外的成本可以主要通過工藝自動化和更高的數(shù)量來補(bǔ)償。
這一點(diǎn)在韓國汽車零部件制造商Infac的實(shí)踐中已經(jīng)可以看到。該公司最近開始批量生產(chǎn)一種用于電動汽車的塑料電池模塊外殼。據(jù)特殊化學(xué)品集團(tuán)朗盛公司的說法,Infac公司使用了朗盛自有品牌Durethan的無鹵素、阻燃和玻璃纖維增強(qiáng)的聚酰胺6(PA6),這是一種易于組合的高性能塑料,也被用于制動踏板和油盤。
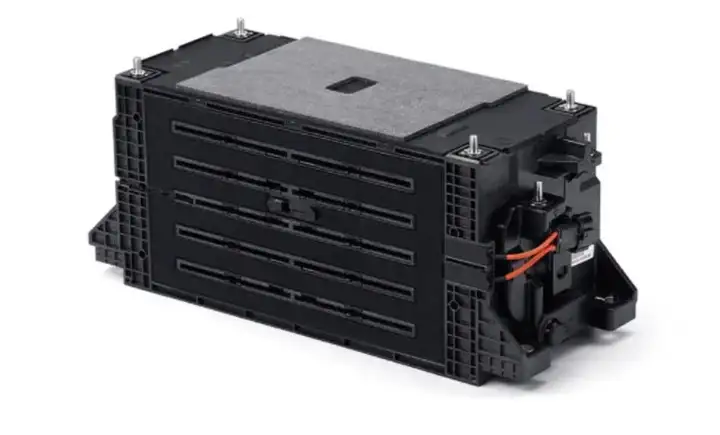

以分鐘為節(jié)拍的混合構(gòu)件生產(chǎn)
從生產(chǎn)的角度來看,始終是成本問題拖累了混合材料的大規(guī)模使用。與傳統(tǒng)材料和工藝相比,周期時(shí)間短、材料循環(huán)不足和耗時(shí)的預(yù)定材料組合的預(yù)處理削弱了連續(xù)纖維增強(qiáng)復(fù)合材料和混合組件的競爭實(shí)力。
德國德累斯頓大學(xué)的輕量化和塑料技術(shù)研究所帶來了一線希望。由汽車供應(yīng)商博澤牽頭的一個(gè)項(xiàng)目聯(lián)盟建立了一個(gè)用于批量生產(chǎn)高負(fù)載的混合材料組件全自動化的工藝鏈——德國宇航中心研究所的工藝開發(fā)中心現(xiàn)在宣布調(diào)試成功。
該系統(tǒng)基于一種注塑組合工藝,其中深拉金屬嵌件與預(yù)制的連續(xù)纖維增強(qiáng)補(bǔ)丁相結(jié)合,然后用短纖維增強(qiáng)塑料進(jìn)行包覆。所有的工藝參數(shù)和工藝步驟都由一個(gè)中央控制單元通過350個(gè)傳感器通道進(jìn)行監(jiān)測和協(xié)調(diào)。
從金屬嵌件的精確溫度控制到促進(jìn)粘合的等離子涂層和使用纖維增強(qiáng)貼片壓制的過程,都是針對循環(huán)時(shí)間小于一分鐘的大規(guī)模生產(chǎn)要求量身定制的。

在材料領(lǐng)域中的競賽還在繼續(xù)
然而,碳纖維部件的失分并沒有讓汽車工業(yè)輕量化的倡導(dǎo)者偏離正軌。在候選材料鋼、鋁、鎂和復(fù)合材料中,汽車制造商根本沒有明確的最愛。
例如,大眾汽車的模塊化電驅(qū)動矩陣(MEB)除了高強(qiáng)度鋼外,還包含許多其他輕量化結(jié)構(gòu),包括鋁制門檻板、超高強(qiáng)度座椅橫梁、薄型、高強(qiáng)度外門板、塑料后擋板和鋁制電池外殼。
在奔馳汽車公司,接近量產(chǎn)的概念車型 EQXX 也高度關(guān)注輕量化,畢竟奔馳這樣的傳統(tǒng)團(tuán)隊(duì)關(guān)注的是全電動汽車在續(xù)航里程方面的優(yōu)勢。
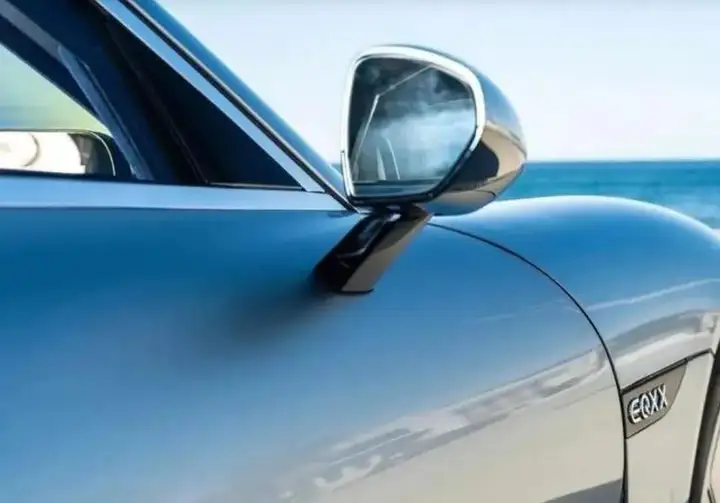
奔馳汽車工程師們針對 EQ 系列采取的輕量化措施旨在減輕 100 kWh 電池組以及車身和內(nèi)部區(qū)域的重量。除了使用鋼材外,還有許多由鋁、鎂制成的組件以及由玻璃纖維和碳纖維增強(qiáng)塑料基體制成的組件和補(bǔ)丁。目標(biāo)之一:電池體積更小、重量減輕 30%,每次充電可行駛 1000 公里。(來源:輕量化技術(shù)網(wǎng)、EV世紀(jì)、榮格等)
版權(quán)聲明:復(fù)材云集尊重版權(quán)并感謝每一位作者的辛苦付出與創(chuàng)作;除無法溯源的文章,我們均在文末備注了來源;如文章視頻、圖片、文字涉及版權(quán)問題,請第一時(shí)間聯(lián)系我們,我們將根據(jù)您提供的證明材料確認(rèn)版權(quán)并按國家標(biāo)準(zhǔn)支付稿酬或立即刪除內(nèi)容!