碳纖維
性能優(yōu)異工業(yè)材料,制造全環(huán)節(jié)技術(shù)為先
(一)聚丙烯晴碳化及石墨化處理而得,原絲端及復(fù)合材料或?yàn)殛P(guān)鍵
碳纖維是由有機(jī)纖維(主要是聚丙烯腈纖維)經(jīng)碳化及石墨化處理而得到的微晶石墨材料纖維。碳纖維的含碳量在90%以上,具有強(qiáng)度高、質(zhì)量輕、比模量高、耐腐蝕、耐疲勞、熱膨脹系數(shù)小、耐高低溫等優(yōu)越性能,是軍民用重要基礎(chǔ)材料,應(yīng)用于航空航天、體育、汽車、建筑及其結(jié)構(gòu)補(bǔ)強(qiáng)等領(lǐng)域。樹脂基碳纖維模量高于鈦合金等傳統(tǒng)工業(yè)金屬材料,強(qiáng)度通過設(shè)計(jì)可達(dá)到高強(qiáng)鋼水平,明顯高于鈦合金,在性能和輕量化兩方面優(yōu)勢(shì)都較為明顯。
碳纖維成本也相對(duì)較高,雖然目前在航空航天等高精尖領(lǐng)域已部分取代傳統(tǒng)材料,但對(duì)力學(xué)性能要求相對(duì)不高的傳統(tǒng)行業(yè)則更看重經(jīng)濟(jì)效益,傳統(tǒng)材料依然為主力軍。
全產(chǎn)業(yè)鏈看,制造碳纖維產(chǎn)品的上游原絲端與中游復(fù)合材料均是碳纖維產(chǎn)業(yè)鏈的核心環(huán)節(jié),整個(gè)制造的全環(huán)節(jié)技術(shù)壁壘均高。作為碳纖維的前驅(qū)體,高質(zhì)量的PAN原絲是制備高性能碳纖維的前提條件,但其中的聚合、紡絲、碳化、氧化等工藝并非朝夕能夠達(dá)成,其產(chǎn)業(yè)化工藝以及反應(yīng)裝置核心技術(shù)是關(guān)鍵。

(二)大小絲束分類易于區(qū)分下游市場(chǎng),質(zhì)量過關(guān)的原絲是產(chǎn)業(yè)化前提
處于上游的碳纖維分類方式較多,可按照絲束大小分為小絲束和大絲束,該分類方式易于區(qū)分其下游市場(chǎng)。小絲束主要是指24K以下(指碳纖維絲束中單絲數(shù)量,1K=1000根),因其性能較為優(yōu)異,常用于航空航天等領(lǐng)域。大絲束目前常為36K、48K,因其碳纖維粘連、斷絲等現(xiàn)象較多,使強(qiáng)度、剛度受到影響,所以性能相對(duì)較低、分散性也較大。但大絲束碳纖維生產(chǎn)成本較低,部分性能優(yōu)于小絲束,48K大絲束最大的優(yōu)勢(shì),生產(chǎn)和應(yīng)用效率高,可以大幅度實(shí)現(xiàn)低成本的目標(biāo),從而打破碳纖維高昂價(jià)格帶來的應(yīng)用局限。故大絲束碳纖維被稱為"工業(yè)級(jí)"碳纖維,主要應(yīng)用于汽車、風(fēng)電等工業(yè)領(lǐng)域。
碳纖維制備過程中,質(zhì)量過關(guān)的原絲是產(chǎn)業(yè)化的前提。碳纖維的強(qiáng)度顯著地依賴于原絲的致密性和微觀形態(tài)結(jié)構(gòu),質(zhì)量過關(guān)的原絲是實(shí)現(xiàn)產(chǎn)業(yè)化的前提,是穩(wěn)定生產(chǎn)的基礎(chǔ)。目前,比較常用的紡絲工藝是濕法紡絲、干濕法(干噴濕紡)紡絲。在致密性方面,干噴濕紡紡絲工藝是高性能碳纖維原絲的主流制備方法,且成本相比于濕法較低。
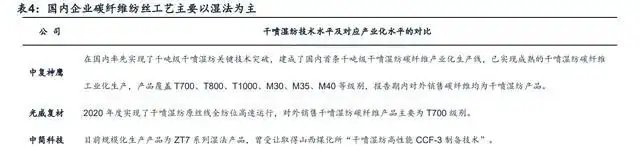
(三)高模高強(qiáng)為碳纖維技術(shù)發(fā)展方向,復(fù)合材料為下游應(yīng)用主要形式
碳纖維技術(shù)發(fā)展至今已經(jīng)歷三代變遷,同時(shí)實(shí)現(xiàn)高拉伸強(qiáng)度和彈性模量是目前碳纖維研制過程中的技術(shù)難點(diǎn)。近年來日美從兩條不同技術(shù)路徑在第三代碳纖維上取得技術(shù)突破,并有望在未來5-10年內(nèi)實(shí)現(xiàn)工業(yè)化生產(chǎn),對(duì)于提高戰(zhàn)機(jī)、武器的作戰(zhàn)能力意義重大。
東麗利用傳統(tǒng)的PAN溶液紡絲技術(shù)使碳纖維強(qiáng)度和彈性模量都得到較大提升:通過精細(xì)控制碳化過程,在納米尺度上改善碳纖維的微結(jié)構(gòu),對(duì)碳化后纖維中石墨微晶取向、微晶尺寸、缺陷等進(jìn)行控制。
以東麗較為先進(jìn)的T1100G為例,T1100G的拉伸強(qiáng)度和彈性模量分別為6.6GPa和324GPa,比T800提高12%以及10%,正進(jìn)入產(chǎn)業(yè)化階段。美國(guó)佐治亞理工學(xué)院從原絲制備工藝入手,利用創(chuàng)新的PAN基碳纖維凝膠紡絲技術(shù),通過凝膠把聚合物聯(lián)結(jié)在一起,產(chǎn)生強(qiáng)勁的鏈內(nèi)力和微晶取向的定向性,保證在高彈性模量所需的較大微晶尺寸情況下,仍具備高強(qiáng)度,將碳纖維拉伸強(qiáng)度提升至5.5~5.8GPa,拉伸彈性模量達(dá)354~375GPa。
碳纖維復(fù)合材料是下游市場(chǎng)的應(yīng)用形式。復(fù)合材料是由兩種或兩種以上不同性質(zhì)的材料,通過物理或化學(xué)的方法,在宏觀上組成具有新性能的材料。各種材料在性能上互相取長(zhǎng)補(bǔ)短,產(chǎn)生協(xié)同效應(yīng),使復(fù)合材料的綜合性能優(yōu)于原組成材料以滿足各種不同的要求。復(fù)合材料根據(jù)不同物相在空間上的連續(xù)性,可以將其分為基體與增強(qiáng)材料。一般而言,碳纖維不單獨(dú)應(yīng)用于下游領(lǐng)域,常作為增強(qiáng)材料形成復(fù)合材料。
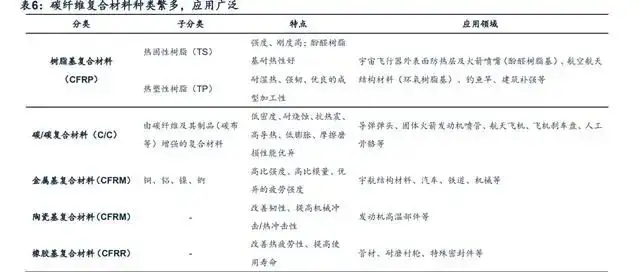
碳纖維復(fù)合材料的制備難度,一方面在于基體樹脂材料的選擇,另一方面在于成型技術(shù)。基體樹脂材料的性能以及相對(duì)應(yīng)的與碳纖維的配套體系,決定的是材料設(shè)計(jì)環(huán)節(jié)。但在該環(huán)節(jié)完成之后,無論制作試樣還是量產(chǎn),都離不開成型以及相關(guān)技術(shù),雖然實(shí)際上兩個(gè)環(huán)節(jié)不能完全分開。
成型加工過程賦予材料一定的形態(tài),使之體現(xiàn)出必要的特性,與此同時(shí),碳纖維復(fù)合材料成型中部分技術(shù)的成功實(shí)現(xiàn),是碳纖維在商業(yè)航空領(lǐng)域得以規(guī)模化應(yīng)用的前提。用于航空航天領(lǐng)域的CFRP構(gòu)件此前大多使用預(yù)浸料工藝,但是預(yù)浸料工藝的成本較高,因預(yù)浸料的裁減和鋪疊過程是人工成本和工藝時(shí)間消耗最大的環(huán)節(jié)。
為改進(jìn)這一情況,飛機(jī)制造商與材料供應(yīng)商共同研究開發(fā)出了自動(dòng)鋪放成型技術(shù),達(dá)到了通過自動(dòng)化和高速化完成對(duì)大型復(fù)合材料部件的成型、提高生產(chǎn)效率、降低生產(chǎn)成本的目的。通常使用鋪放成型技術(shù)可以比其他的成型工藝減少成本至少30%~50%。正是由于自動(dòng)鋪放成型技術(shù)的出現(xiàn),CFRP在商用客機(jī)上的規(guī)模化應(yīng)用才能夠成為現(xiàn)實(shí)。
國(guó)內(nèi)自動(dòng)復(fù)合材料自動(dòng)鋪放技術(shù)取得進(jìn)展。飛機(jī)復(fù)合材料主承力構(gòu)件主要采用預(yù)浸料成形技術(shù)制造,而自動(dòng)鋪放成形是替代人工鋪疊、提高質(zhì)量和生產(chǎn)效率的關(guān)鍵,在制造大型復(fù)合材料構(gòu)件時(shí)優(yōu)勢(shì)極為突出。
國(guó)外自動(dòng)鋪放技術(shù)雖已成熟,但仍在不斷發(fā)展和進(jìn)步,并通過開發(fā)新技術(shù)來實(shí)現(xiàn)復(fù)合材料構(gòu)件低成本高效益制造;中國(guó)國(guó)內(nèi)自動(dòng)鋪放技術(shù)起步10多年,已有了長(zhǎng)足進(jìn)步,技術(shù)成熟度在不斷提高。
中航復(fù)材材料有限責(zé)任公司“在國(guó)內(nèi)率先將數(shù)字化下料、激光投影和自動(dòng)鋪帶技術(shù)應(yīng)用于型號(hào)產(chǎn)品的研制和批量生產(chǎn),降低了成本,縮短了制造周期,保證了產(chǎn)品的質(zhì)量穩(wěn)定性和一致性,縮短了與發(fā)達(dá)國(guó)家的水平差距”。綜合來看,國(guó)內(nèi)在基體樹脂材料、成型工藝技術(shù)方面仍有較大的進(jìn)步空間。
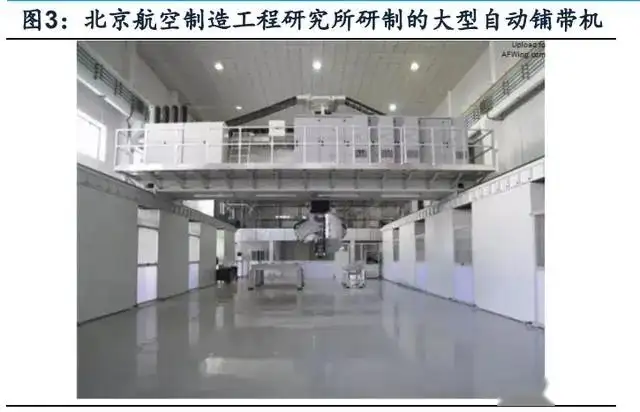
市場(chǎng)
高端領(lǐng)域重性能,中低端領(lǐng)域成本競(jìng)爭(zhēng)
(一)商業(yè)模式:市場(chǎng)需求差異下高低端市場(chǎng)驅(qū)動(dòng)力不同
高端市場(chǎng)對(duì)碳纖維及其復(fù)合材料有高性能要求,尤其在航空航天等高端裝備領(lǐng)域,而中低端領(lǐng)域成本競(jìng)爭(zhēng)較為激烈。具體看,航空航天領(lǐng)域高端裝備及民航碳纖維商業(yè)模式及驅(qū)動(dòng)力存在一定差異。航空高端裝備對(duì)碳纖維的需求更注重性能因素,而民用航空領(lǐng)域關(guān)注直接及間接成本因素。但因技術(shù)難度大、客戶綁定深,航空航天領(lǐng)域總體仍體現(xiàn)為高毛利率特征。
中低端領(lǐng)域?qū)μ祭w維性價(jià)比要求高,成本競(jìng)爭(zhēng)較為激烈。
成本競(jìng)爭(zhēng)一方面體現(xiàn)為下游客戶議價(jià)權(quán)較強(qiáng)。在常用的領(lǐng)域如風(fēng)電、建筑材料等,碳纖維復(fù)合材料制造工藝相對(duì)簡(jiǎn)單,且下游風(fēng)電整機(jī)廠商客戶較為集中,買家議價(jià)權(quán)較強(qiáng),可在碳纖維產(chǎn)業(yè)鏈中的不同環(huán)節(jié)選定不同供應(yīng)商。如風(fēng)電廠商維斯塔斯幫助光威復(fù)材協(xié)調(diào)部分碳纖維從臺(tái)塑進(jìn)口,體現(xiàn)對(duì)成本以及分散上游供應(yīng)商集中度的考量。
成本競(jìng)爭(zhēng)的另外一方面常體現(xiàn)為碳纖維生產(chǎn)商主動(dòng)綁定大客戶。碳纖維整體具有顯著的規(guī)模效應(yīng),產(chǎn)量的增加利于提高碳纖維制造商的盈利能力,綁定大客戶利于借助其市場(chǎng)需求較為穩(wěn)定的增長(zhǎng)充分發(fā)揮規(guī)模優(yōu)勢(shì)。
此外,雖然碳纖維具有較優(yōu)異性能,但由于多數(shù)客戶仍出于對(duì)“新事物”的擔(dān)憂,以及碳纖維復(fù)合材料的可設(shè)計(jì)性導(dǎo)致需要與客戶進(jìn)行深度綁定以最大化發(fā)揮碳纖維性能,碳纖維應(yīng)用范圍現(xiàn)階段仍然受一定限制。
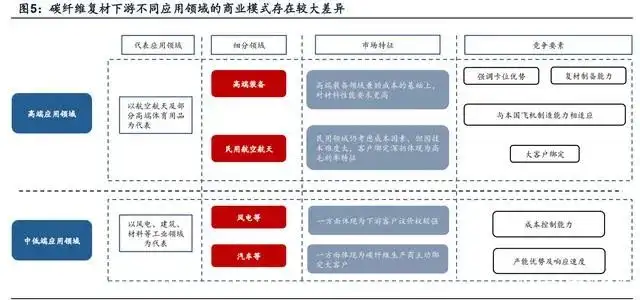
民用航天航空領(lǐng)域,兼顧性能及成本。
一方面,民用航空由于安全性是首要考量的因素,材料廠商需要在前期進(jìn)入飛機(jī)設(shè)計(jì)環(huán)節(jié),與飛機(jī)整機(jī)設(shè)計(jì)商與制造商共同接受適航審查,無形中體現(xiàn)了卡位優(yōu)勢(shì),也加寬了民航產(chǎn)業(yè)鏈碳纖維制造企業(yè)護(hù)城河。例如,日本東麗T700系列碳纖維的研制,是針對(duì)波音公司對(duì)民機(jī)減重的要求下,對(duì)部分承力構(gòu)件進(jìn)行輕量化設(shè)計(jì)的過程中所提出的要求而進(jìn)行開發(fā)的。
另一方面,民航制造商因航油價(jià)格高昂,達(dá)到輕量化目的的需求比其他領(lǐng)域更為強(qiáng)烈。當(dāng)成本端達(dá)到制造成本低于后期節(jié)省燃油費(fèi)用時(shí),民用航空領(lǐng)域大規(guī)模使用碳纖維復(fù)合材料才成為可能。據(jù)上文所述,航空用碳纖維預(yù)浸料自動(dòng)鋪疊技術(shù)的成功商業(yè)化,是民航規(guī)模化使用碳纖維復(fù)合材料的前提。后期隨著碳纖維復(fù)合材料制備工藝的提升,民用航空上使用比例有望逐步提高。
中低端產(chǎn)品以工業(yè)領(lǐng)域?yàn)橹鳎詢r(jià)比要求更高,成本競(jìng)爭(zhēng)激烈。由于技術(shù)壁壘,大絲束碳纖維制造的核心技術(shù)基本上還是被美日壟斷把控,但國(guó)內(nèi)企業(yè)已逐漸重視大絲束碳纖維領(lǐng)域的產(chǎn)業(yè)化。
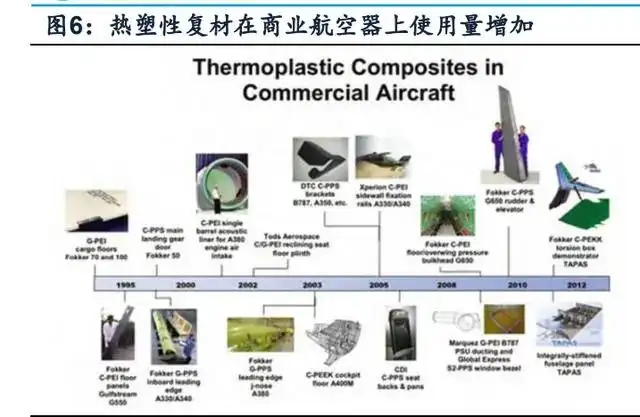
從成本結(jié)構(gòu)來看,原材料與能耗構(gòu)成碳纖維主要成本。能耗是PAN碳纖維總成本中最高的部分,約占34%。而且碳纖維成本對(duì)于能源價(jià)格變動(dòng)最為敏感,能源價(jià)格每千瓦時(shí)變動(dòng)0.01歐元,每千克碳纖維成本變動(dòng)0.83歐元。其次是前驅(qū)體所用原料成本,即丙烯腈、甲基丙烯酸酯、衣康酸,占比約19%,其中丙烯腈每千克價(jià)格變動(dòng)0.01歐元?jiǎng)t碳纖維成本每千克變動(dòng)0.02歐元。最后是設(shè)備的攤銷成本占約18%。
發(fā)揮規(guī)模優(yōu)勢(shì)是短期降成本的主要路徑,尋找性價(jià)比高的前驅(qū)體(PAN原絲)、提高轉(zhuǎn)化過程中的工藝技術(shù)以及垂直整合下游則屬于長(zhǎng)期降低成本的主要思路。
(1)通過擴(kuò)大工廠規(guī)模和生產(chǎn)線規(guī)模可以顯著碳纖維制造降低成本;
(2)尋找原材料替代品,比如以木質(zhì)素(硬木或軟木)作為替代PAN原絲的資源可降低成本;
(3)在原絲轉(zhuǎn)化成碳纖維的轉(zhuǎn)化過程,通過使用先進(jìn)的氧化碳化設(shè)備和加工工藝,優(yōu)化表面處理過程可降低成本;
(4)整合下游產(chǎn)業(yè)從而減少中間環(huán)節(jié)成本,比如SGL集團(tuán)與德國(guó)寶馬公司共同投資建設(shè)低成本碳纖維工廠,以及日本東麗集團(tuán)、三菱公司也與豐田汽車公司達(dá)成合作,希望開發(fā)新一代低成本碳纖維復(fù)合材料直接運(yùn)用到下游汽車產(chǎn)業(yè)中,減少中間無謂損失以降低最終產(chǎn)品的成本。
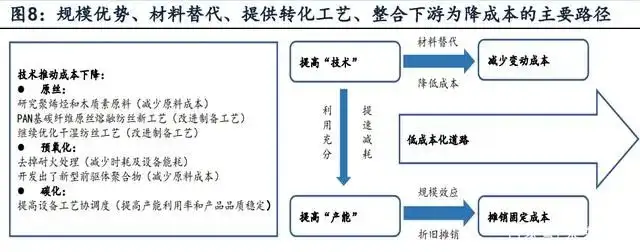
碳纖維行業(yè)具有明顯規(guī)模效應(yīng),擴(kuò)大生產(chǎn)規(guī)模利于降低碳纖維主要制造環(huán)節(jié)的成本。在碳纖維的制備過程中,相比于基準(zhǔn)產(chǎn)量,通過擴(kuò)大產(chǎn)能各環(huán)節(jié)單位成本均有下降:原絲工序環(huán)節(jié)的單位成本可降低8%,穩(wěn)定化與氧化降低36%,碳化、石墨化降低36%,表面整理降低11%,卷曲與包裝降低33%,其中擴(kuò)產(chǎn)對(duì)氧化碳化高能耗工序降成本效果更為明顯,規(guī)模效益顯著。
以中簡(jiǎn)科技為例,其主營(yíng)業(yè)務(wù)的成本構(gòu)成中制造費(fèi)用占比較高,制造費(fèi)用主要為生產(chǎn)環(huán)節(jié)的資產(chǎn)折舊與攤銷,以及燃料、動(dòng)力、蒸汽等支出。2018-2020年制造費(fèi)用占主營(yíng)業(yè)務(wù)成本的比重分別為73.22%、76.28%及75.53%。主要原因是碳纖維生產(chǎn)具有占地面積大、設(shè)備價(jià)值高的特點(diǎn),各期折舊攤銷較大,以及碳纖維生產(chǎn)所需的能源消耗較大,導(dǎo)致制造費(fèi)用占比較高。因而在短期內(nèi),擴(kuò)大產(chǎn)能、提高產(chǎn)能利用率是降低成本的重要途徑。
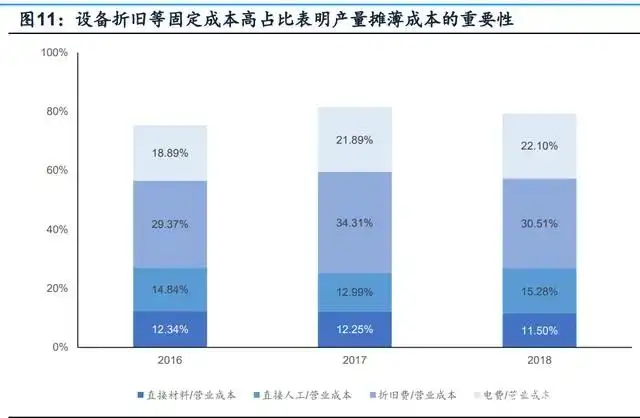
優(yōu)化原絲制造工藝可以提高生產(chǎn)效率,縮短工序耗時(shí)長(zhǎng)度,從而擴(kuò)大產(chǎn)量降低攤銷成本,短期看干濕法紡絲仍然是主流,但長(zhǎng)期或被PAN基碳纖維原絲熔融紡絲工藝等取代。
美國(guó)的橡樹嶺國(guó)家實(shí)驗(yàn)室從2007年開始一直致力于尋找低成本原材料,相繼開發(fā)了聚烯烴和木質(zhì)素原料的碳纖維前驅(qū)體。但由于開發(fā)難度大,實(shí)現(xiàn)擴(kuò)產(chǎn)成熟運(yùn)用還有一定難度。
在同樣的紡絲裝備及能源消耗條件下,干濕法紡絲的綜合產(chǎn)量是濕法紡絲的2-8倍,PAN基碳纖維絲束的生產(chǎn)成本可降低75%。以中簡(jiǎn)科技2018年測(cè)算,除折舊外的一切費(fèi)用與產(chǎn)量成比例增長(zhǎng),折舊費(fèi)暫且保持不變的情況下,全部用干濕法保守估計(jì)有望使單位碳纖維成本下降15%-27%。
參考TextileStudyCenter,熔紡紡織速度達(dá)2500-3000ft/min,而濕紡速度僅為150-300ft/min,生產(chǎn)效率的優(yōu)勢(shì)實(shí)現(xiàn)了熔紡工藝的成本改進(jìn)。
注重制造設(shè)備的自研,提高設(shè)備和工藝匹配度從而提高產(chǎn)能利用率來降低成本。碳纖維自研發(fā)以來一直被視為高端裝備用材料,因此西方國(guó)家對(duì)我國(guó)實(shí)行嚴(yán)格的技術(shù)和設(shè)備禁運(yùn)。
日系公司則通過對(duì)碳纖維關(guān)鍵產(chǎn)品的技術(shù)禁運(yùn),對(duì)通用型產(chǎn)品進(jìn)行低價(jià)擠壓,從而壓制國(guó)內(nèi)碳纖維的研發(fā)進(jìn)展。據(jù)賽奧碳纖維技術(shù),2020年我國(guó)碳纖維企業(yè)的產(chǎn)能利用率在50%左右,較2017年已有較大提升。中國(guó)目前已跨越了低達(dá)產(chǎn)率的歷史階段,水平正趨近國(guó)際水平,但仍有提升空間。
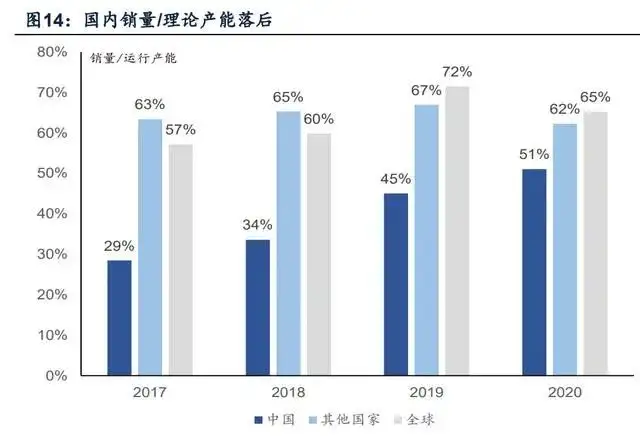
與此同時(shí),國(guó)外龍頭企業(yè)大多形成全產(chǎn)業(yè)鏈覆蓋,有利于降低成本,而國(guó)內(nèi)企業(yè)產(chǎn)業(yè)鏈的各個(gè)環(huán)節(jié)較為分散。由于碳纖維行業(yè)具有高資本投入和高技術(shù)壁壘,國(guó)外龍頭企業(yè)起步早、技術(shù)強(qiáng),設(shè)備、工藝、材料等大多屬于自主研發(fā),一般實(shí)現(xiàn)從原絲到下游市場(chǎng)全產(chǎn)業(yè)鏈覆蓋并形成部分產(chǎn)品內(nèi)銷降低周轉(zhuǎn)成本,并在產(chǎn)品上形成差異化競(jìng)爭(zhēng),而國(guó)內(nèi)企業(yè)環(huán)節(jié)較為分散。
碳纖維復(fù)合材料設(shè)備多由美國(guó)公司壟斷,如自動(dòng)鋪絲機(jī)、層合固化裝備等,上述原因使得我國(guó)碳纖維復(fù)合材料整體上尚處于起步階段。國(guó)內(nèi)部分公司雖然具備一定生產(chǎn)復(fù)合材料的能力,但相比于全球領(lǐng)先企業(yè),仍然存在一定的差距。
(二)市場(chǎng)空間:下游以CFRP應(yīng)用為主,因需求差異致天花板有別
CFRP應(yīng)用場(chǎng)景廣泛,應(yīng)用比例提高,市場(chǎng)空間廣闊。碳纖維復(fù)合材料是指至少有一種增強(qiáng)材料是碳纖維的復(fù)合材料,其中最常見的是樹脂基碳纖維復(fù)合材料(CFRP)。由于CFRP比強(qiáng)度、比彈性模量等機(jī)械性能,以及耐疲勞性、穩(wěn)定性等相比傳統(tǒng)材料有明顯優(yōu)勢(shì),因此在很多領(lǐng)域內(nèi)對(duì)金屬材料,尤其是輕質(zhì)金屬材料形成競(jìng)爭(zhēng)取代的局面。
CFRP應(yīng)用場(chǎng)景廣泛,在航空航天和體育休閑領(lǐng)域率先形成大規(guī)模市場(chǎng),而隨著21世紀(jì)以來碳纖維及其復(fù)合材料制造成本不斷下降,在汽車制造、風(fēng)力發(fā)電等領(lǐng)域應(yīng)用比例在不斷提高。
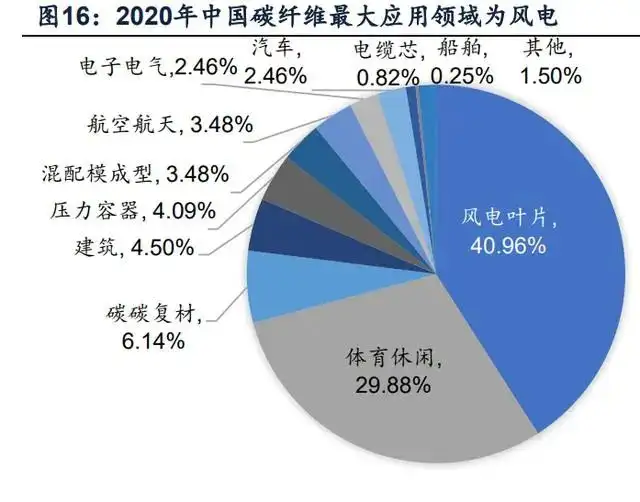
CFRP下游市場(chǎng)差異化的需求和制造特征使得不同領(lǐng)域碳纖維的性能、成本均有所差異,各個(gè)市場(chǎng)的驅(qū)動(dòng)力及潛在天花板也有所不同。KSI是機(jī)械強(qiáng)度單位,表示單位面積上所能承受的壓力。
按成本效果分類,當(dāng)碳纖維處在500-750KSI,即30-35MSI時(shí),稱其為中性類別,此時(shí)需要在材料的成本和表現(xiàn)之間相權(quán)衡;當(dāng)碳纖維處在250-500KSI,即<30MSI時(shí),稱其為高量類別,材料對(duì)成本比較敏感。中性類別碳纖維可應(yīng)用于壓力容器領(lǐng)域,例如氫氣、天然氣等的存儲(chǔ);高量類別碳纖維可用于汽車部件,通過減重降低燃料消耗;兩種碳纖維還應(yīng)用于風(fēng)電葉片、油氣管道、電力傳輸?shù)阮I(lǐng)域,目前用量受成本和制造方法等多因素制約。
航空材料發(fā)展至今歷經(jīng)四代變遷,復(fù)合材料將是未來飛機(jī)首選的航空結(jié)構(gòu)主要材料。航空領(lǐng)域常常率先使用先進(jìn)材料以提高裝備性能,從鋼鐵到鋁合金到鈦合金到碳纖維等復(fù)合材料,未來碳纖維等復(fù)合材料比重將不斷擴(kuò)大。
第一代航空材料以木、布為主,由于強(qiáng)度較低,很快轉(zhuǎn)變?yōu)榈诙匿摗X金屬結(jié)構(gòu),鋁合金密度更小,有利于提高飛機(jī)的強(qiáng)度和安全性;第三代航空材料加入了鈦合金材料,具有高耐熱性和更高的強(qiáng)度,首先被應(yīng)用于耐高溫部件并向其他部件擴(kuò)展;第四代和第五代航空材料始于碳纖維的成功制備,碳纖維復(fù)合材料具有高強(qiáng)度、高模量、輕量化的優(yōu)點(diǎn),不斷廣泛運(yùn)用于飛機(jī)的部分部件,并對(duì)傳統(tǒng)金屬實(shí)現(xiàn)一定程度的替代。
航空航天材料逐步邁入碳纖維復(fù)合材料時(shí)代,復(fù)合材料應(yīng)用不斷擴(kuò)大。碳纖維復(fù)合材料具有高強(qiáng)度、高模量、輕量化的優(yōu)點(diǎn),目前逐步運(yùn)用于飛機(jī)部件并對(duì)傳統(tǒng)金屬實(shí)現(xiàn)一定替代。
在航空航天領(lǐng)域,為達(dá)到飛行器輕量化的目標(biāo),實(shí)現(xiàn)增加有效載荷,降低燃料費(fèi)用,以CFRP為代表的先進(jìn)復(fù)合材料的使用量逐年擴(kuò)大。近年來,無論是在單機(jī)上所占的比例還是總使用量,CFRP應(yīng)用范圍逐步擴(kuò)張,在飛機(jī)上使用CFRP等先進(jìn)復(fù)合材料,不僅是由于其可以大幅減輕機(jī)身重量,而且在耐腐蝕以及抗疲勞性能等方面與傳統(tǒng)合金金屬相比也有較大的優(yōu)勢(shì)。
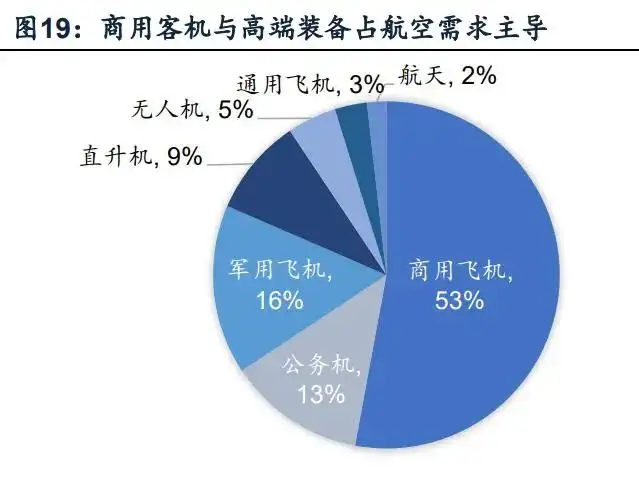
CFRP的大范圍應(yīng)用通常是由航空高端裝備引導(dǎo),民用客機(jī)領(lǐng)域空客、波音先行。先進(jìn)復(fù)合材料在F-15戰(zhàn)斗機(jī)上首次實(shí)現(xiàn)應(yīng)用時(shí),其在整個(gè)飛機(jī)結(jié)構(gòu)材料中所占的重量比例不過2%,但是到了F/A18E/F戰(zhàn)斗機(jī),其比例已經(jīng)達(dá)到了19%。
此外,F(xiàn)-22戰(zhàn)斗機(jī)單機(jī)使用了350個(gè)以上的碳纖維復(fù)合材料零部件,達(dá)到了機(jī)身空重的25%,其中纖維增強(qiáng)熱固性樹脂為24%,另有1%的纖維增強(qiáng)熱塑性樹脂材料。單機(jī)使用碳纖維總量接近4t,其中強(qiáng)度在5.08GPa以上的產(chǎn)品占到80%以上,主要用于機(jī)翼中間梁和后梁、垂直尾翼邊緣和方向舵、水平穩(wěn)定器、升降舵、機(jī)身框架、壁板、加強(qiáng)框、油箱框架等關(guān)鍵位置和部件。使用的碳纖維全部來源于Cytec和Hexcel兩家美國(guó)公司,樹脂基體材料主要是環(huán)氧樹脂和雙馬來酰亞胺樹脂。通過使用RTM的先進(jìn)成型方法,F(xiàn)-22戰(zhàn)斗機(jī)成功證明了CFRP部件不僅可以在性能上滿足要求,而且在成本控制上也具有可行性和很大的潛力。
高性能碳纖維政策加碼,利于推進(jìn)國(guó)內(nèi)碳纖維產(chǎn)業(yè)建設(shè)。高強(qiáng)度、高模量、低比重特點(diǎn)的碳纖維增強(qiáng)復(fù)合材料成為各類軍、民裝備最重要的候選材料之一,已成為航空以及國(guó)防裝備的關(guān)鍵材料。復(fù)合材料的用量是衡量高端裝備先進(jìn)性的重要標(biāo)志。
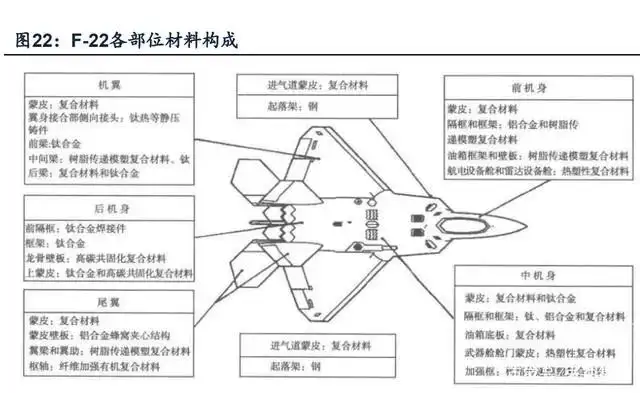
民機(jī)上,NASA研究表明飛機(jī)上使用CFRP的制造成本不會(huì)超過其節(jié)省的運(yùn)行成本。民用飛機(jī)在保證乘客乘坐體驗(yàn)的同時(shí),要盡可能地提高飛機(jī)的經(jīng)營(yíng)效率,飛機(jī)空重的減少可以提高燃油效率從而降低直接運(yùn)行成本。
世界領(lǐng)先民用飛機(jī)制造商波音和空客在碳纖維應(yīng)用上引領(lǐng)著行業(yè)方向。波音公司B787客機(jī)機(jī)體構(gòu)造的50%使用了碳纖維復(fù)合材料,每架約為35噸。波音公司在該產(chǎn)品手冊(cè)中表示,應(yīng)用碳纖維相比同體積傳統(tǒng)材料的飛機(jī)減重了40000磅,B787也因此將燃油效率提高了20%,減少了20%的廢氣排放。緊接著空客公司對(duì)A350進(jìn)行重新設(shè)計(jì),將新飛機(jī)改名為A350XWB,其主翼、機(jī)身、尾翼全部使用復(fù)合材料,占機(jī)身重量的53%。
遠(yuǎn)期看,國(guó)產(chǎn)飛機(jī)民航市場(chǎng)有望成為國(guó)內(nèi)高性能碳纖維企業(yè)的潛在增長(zhǎng)點(diǎn)之一。民用飛機(jī)在保證乘客乘坐體驗(yàn)的同時(shí),要盡可能地提高飛機(jī)的經(jīng)營(yíng)效率,飛機(jī)空重的減少可以提高燃油效率從而降低直接運(yùn)行成本。世界領(lǐng)先民用飛機(jī)制造商波音和空客在碳纖維應(yīng)用上引領(lǐng)著行業(yè)方向。
根據(jù)波音公司官網(wǎng),波音公司B787客機(jī)機(jī)體構(gòu)造的50%由碳纖維復(fù)合材料構(gòu)成,主體結(jié)構(gòu)的絕大部分由復(fù)合材料構(gòu)成,尤其是機(jī)身部分。
空客公司A350F也使用了大量的碳纖維復(fù)合材料,機(jī)翼,中央翼箱和機(jī)身面板主要由復(fù)合材料制成。這些材料選擇使飛機(jī)更輕、更硬、更堅(jiān)固、更有能力和更具成本效益,同時(shí)提高了耐腐蝕性和抗疲勞性,從而降低了維護(hù)要求。
空客公司計(jì)算得出,應(yīng)用碳纖維復(fù)合材料使得A350F在起飛時(shí)的重量減少了約28噸,飛行燃料消耗減少了約20%,并且降低了著陸和導(dǎo)航費(fèi)用。
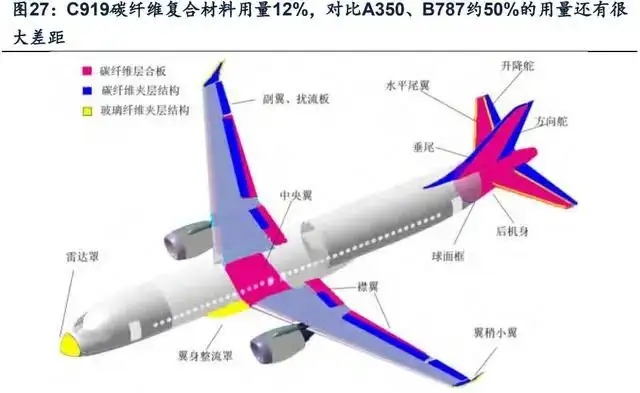
風(fēng)力發(fā)電建設(shè)刺激碳纖維需求,大絲束契合低成本特性。CFRP與使用傳統(tǒng)玻璃纖維增強(qiáng)材料相比,可以達(dá)到20%-30%的減重效果,同時(shí)剛性和強(qiáng)度更加優(yōu)異,通過采用氣動(dòng)效率更高的薄翼型和增加葉片長(zhǎng)度,能提高風(fēng)能利用率和年發(fā)電量,從而降低綜合使用成本。由于大絲束性價(jià)比高的優(yōu)勢(shì)使得其主要運(yùn)用于工業(yè)風(fēng)電,降價(jià)放量成為領(lǐng)域的驅(qū)動(dòng)力。目前風(fēng)電機(jī)組正朝著大型化、輕量化的方向發(fā)展,超長(zhǎng)的葉片對(duì)材料的強(qiáng)度和剛度提出了更高的要求,使得碳纖維及其復(fù)合材料在風(fēng)電葉片領(lǐng)域使用廣泛。
“雙碳”目標(biāo)成為風(fēng)電下游應(yīng)用市場(chǎng)需求重要驅(qū)動(dòng)力。2020年風(fēng)電葉片首次超過體育休閑市場(chǎng)成為全球碳纖維需求份額最高的細(xì)分市場(chǎng)。
隨著“碳達(dá)峰、碳中和”目標(biāo)的確定,推動(dòng)風(fēng)電行業(yè)發(fā)布《風(fēng)能北京宣言》:“在‘十四五’規(guī)劃中,須為風(fēng)電設(shè)定與碳中和國(guó)家戰(zhàn)略相適應(yīng)的發(fā)展空間:保證年均新增裝機(jī)5000萬千瓦以上。2025年后,中國(guó)風(fēng)電年均新增裝機(jī)容量應(yīng)不低于6000萬千瓦,到2030年至少達(dá)到8億千瓦,到2060年至少達(dá)到30億千瓦。”結(jié)合2020年的需求量,可見下游風(fēng)電應(yīng)用市場(chǎng)需求的拉動(dòng)力量較強(qiáng),疫情沖擊一定程度被中和。
以風(fēng)電為代表新能源行業(yè)景氣度可期。政策端給予鼓勵(lì),據(jù)《國(guó)務(wù)院關(guān)于印發(fā)2030年前碳達(dá)峰行動(dòng)方案的通知》,2030年前碳達(dá)峰行動(dòng)方案中“重點(diǎn)任務(wù)”指出,“大力發(fā)展新能源。全面推進(jìn)風(fēng)電、太陽(yáng)能發(fā)電大規(guī)模開發(fā)和高質(zhì)量發(fā)展,堅(jiān)持集中式與分布式并舉,加快建設(shè)風(fēng)電和光伏發(fā)電基地。
加快智能光伏產(chǎn)業(yè)創(chuàng)新升級(jí)和特色應(yīng)用,創(chuàng)新“光伏+”模式,推進(jìn)光伏發(fā)電多元布局。堅(jiān)持陸海并重,推動(dòng)風(fēng)電協(xié)調(diào)快速發(fā)展,完善海上風(fēng)電產(chǎn)業(yè)鏈,鼓勵(lì)建設(shè)海上風(fēng)電基地。積極發(fā)展太陽(yáng)能光熱發(fā)電,推動(dòng)建立光熱發(fā)電與光伏發(fā)電、風(fēng)電互補(bǔ)調(diào)節(jié)的風(fēng)光熱綜合可再生能源發(fā)電基地。到2030年,風(fēng)電、太陽(yáng)能發(fā)電總裝機(jī)容量達(dá)到12億千瓦以上。”
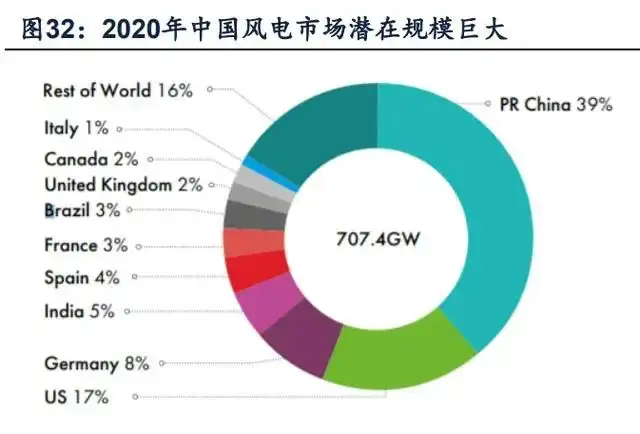
平價(jià)進(jìn)程再提速、需求中樞抬產(chǎn)值。大型化加速疊加零部件價(jià)格回落,21年風(fēng)機(jī)招標(biāo)價(jià)格快速下行,平價(jià)進(jìn)程全面提速。受益21年風(fēng)機(jī)招標(biāo)價(jià)格快速下降,項(xiàng)目收益率大幅提升使得平價(jià)范圍擴(kuò)大,風(fēng)機(jī)招標(biāo)規(guī)模高速增長(zhǎng)。風(fēng)機(jī)交付周期約為一年,上年招標(biāo)規(guī)模可作為先行指標(biāo)預(yù)測(cè)新增裝機(jī)規(guī)模。
根據(jù)金風(fēng)科技統(tǒng)計(jì),2021年1-9月國(guó)內(nèi)風(fēng)機(jī)招標(biāo)規(guī)模約為41.9GW,同比+115%,其中陸上新增招標(biāo)規(guī)模40.9GW,海上新增招標(biāo)規(guī)模1GW,21年全年招標(biāo)規(guī)模有望達(dá)50GW,奠定風(fēng)電新增裝機(jī)高增長(zhǎng)基礎(chǔ)。預(yù)計(jì)2022年底風(fēng)電裝機(jī)規(guī)模在2021年3.3億千瓦的基礎(chǔ)上增長(zhǎng)至3.8億千瓦。陸風(fēng)已實(shí)現(xiàn)平價(jià),海風(fēng)平價(jià)在即,風(fēng)電項(xiàng)目經(jīng)濟(jì)性提升有望進(jìn)一步提高需求成長(zhǎng)中樞,待大宗原材料價(jià)格平穩(wěn)后,風(fēng)電產(chǎn)值空間將進(jìn)一步打開。
輕量化是賽車和乘用車發(fā)展方向之一。CFRP應(yīng)用于汽車領(lǐng)域,可以實(shí)現(xiàn)車體大幅度的輕量化;由于材料具有良好的耐沖擊性能,提高了乘員的安全性。如在賽車領(lǐng)域,對(duì)于一般的大獎(jiǎng)賽賽道,車體重量每增加20kg,會(huì)使得賽車的單圈成績(jī)下降0.4s,對(duì)F-1排位賽而言意味著落后幾個(gè)身位,而對(duì)正賽而言意味著落后半圈。
通過大量使用復(fù)合材料,賽車的性能得到了顯著的提高。在乘用車領(lǐng)域,在應(yīng)對(duì)全球變暖和油價(jià)提高背景下,各國(guó)對(duì)廢氣排放和燃油效率都提出了要求,如我國(guó)《節(jié)能減排新能源汽車產(chǎn)業(yè)發(fā)展規(guī)劃》要求2020年乘用車平均燃料消耗量降低到5L/百公里。對(duì)于最常見的小型乘用車(車身重量1t-1.5t),200kg的輕量化就可以提高燃油效率約2.5km/L。輕量化是國(guó)內(nèi)外汽車廠商應(yīng)對(duì)能源環(huán)境挑戰(zhàn)的共同選擇,也是汽車產(chǎn)業(yè)可持續(xù)發(fā)展的必經(jīng)之路。
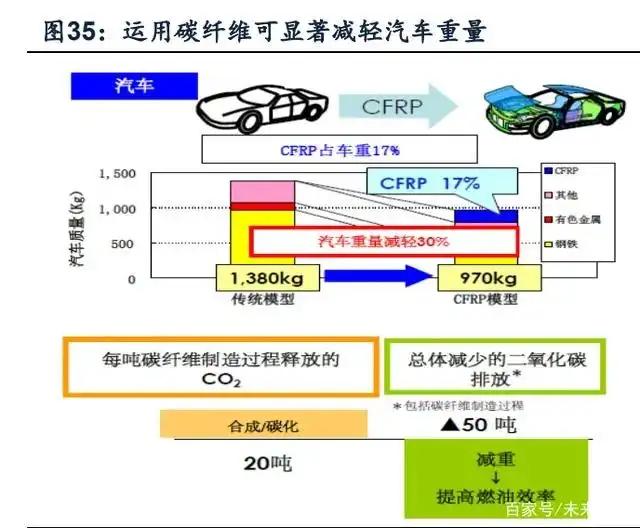
目前由于成本較高,乘用車還未實(shí)現(xiàn)碳纖維的大規(guī)模應(yīng)用,碳纖維性價(jià)比不敵鋁合金。從各項(xiàng)基本力學(xué)性能指標(biāo)來看,即便是通用型的碳纖維復(fù)合材料也遠(yuǎn)遠(yuǎn)優(yōu)于高強(qiáng)度鋼、鋁合金、鈦合金、鎂合金。因此CFRP在以F-1為代表的賽車及其他高級(jí)跑車領(lǐng)域獲得了大量的使用。但碳纖維的原料成本和制造成本過高,在過去很多年一直局限在單值較高且產(chǎn)量較少的領(lǐng)域,沒有拓展到普通乘用車。
在汽車領(lǐng)域,主要采用T300和T700級(jí)別碳纖維小絲束,同時(shí)之后還需要將其打造成為碳纖維復(fù)合材料,附加值又繼續(xù)增加,制備工藝難度大及原絲成本高,使得碳纖維的生產(chǎn)成本遠(yuǎn)高于鋼鐵。隨著技術(shù)進(jìn)步、低成本碳纖維和成型方法取得進(jìn)展,CFRP開始出現(xiàn)在底盤和車身框架等主承力部件。例如2013年領(lǐng)先上市的寶馬i3電動(dòng)汽車車身全部使用碳纖維復(fù)合材料,帶來了顯著的輕量化效果。大型汽車制造商紛紛與復(fù)合材料制造商締結(jié)聯(lián)盟,美國(guó)能源部下屬橡樹嶺國(guó)家實(shí)驗(yàn)室也聯(lián)合陶氏化學(xué)開發(fā)低成本碳纖維技術(shù),這些合作將促進(jìn)CFRP在汽車領(lǐng)域的應(yīng)用。
汽車輕量化確實(shí)是碳纖維長(zhǎng)期機(jī)遇,但短期發(fā)展桎梏于性價(jià)比。寶馬i3在2013年推出后,到2017年該款車型仍然是市場(chǎng)上唯一真正意義上大規(guī)模使用碳纖維、產(chǎn)量在10000輛/年的汽車。德國(guó)汽車研究中心的研究表明,減重所帶來的能源節(jié)省效應(yīng)沒有達(dá)到預(yù)期,除此之外較長(zhǎng)的生產(chǎn)周期和較高的成本均限制了車用碳纖維的發(fā)展。由于生產(chǎn)周期長(zhǎng)和產(chǎn)量低,碳纖維應(yīng)用范圍限制在高端汽車上。
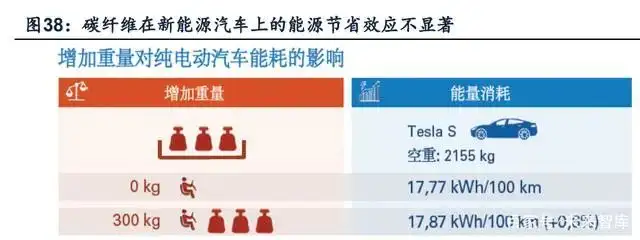
體育休閑是國(guó)內(nèi)碳纖維最早規(guī)模商用、用量最大的領(lǐng)域之一,較早實(shí)現(xiàn)碳纖維產(chǎn)業(yè)化,成本競(jìng)爭(zhēng)或降低市場(chǎng)毛利。高爾夫球桿最初由木材制成,后來發(fā)展到不銹鋼和鋁合金。1972年美國(guó)莎士比亞公司和阿爾迪拉公司率先使用CFRP制作球桿,該材料的球桿扭曲剛性小,擊球方向穩(wěn)定,桿體重量減輕還增加了球的飛行距離。
在釣魚竿上,CFRP材料的應(yīng)用減輕了竿體的重量,同時(shí)提高了剛性和減振性,使得釣魚竿的單手操作變得更加容易,減輕垂釣者的疲勞,數(shù)十年來市場(chǎng)需求穩(wěn)定增長(zhǎng)。使用碳纖維制造的自行車可實(shí)現(xiàn)輕量、高模量和優(yōu)良的沖擊吸收能力,可以緩解由于路面不平帶來的輕微振動(dòng),使騎行過程更為舒適。
碳纖維使體育用品輕量化、提升了機(jī)械性能、改善了用戶的使用體驗(yàn),在主要應(yīng)用場(chǎng)景下實(shí)現(xiàn)了需求的穩(wěn)定增長(zhǎng)。從2017年到2020年,體育應(yīng)用碳纖維市場(chǎng)全球需求量從13,200噸提高到了15,400噸,國(guó)內(nèi)需求量從12,000噸提高到了的14,600噸。不過,近年來體育休閑市場(chǎng)國(guó)際競(jìng)爭(zhēng)激烈,已然從最初的技術(shù)競(jìng)爭(zhēng)轉(zhuǎn)向了成本競(jìng)爭(zhēng)。國(guó)內(nèi)低端碳纖維高成本導(dǎo)致高價(jià)格,在國(guó)際市場(chǎng)上的競(jìng)爭(zhēng)能力有待提升。
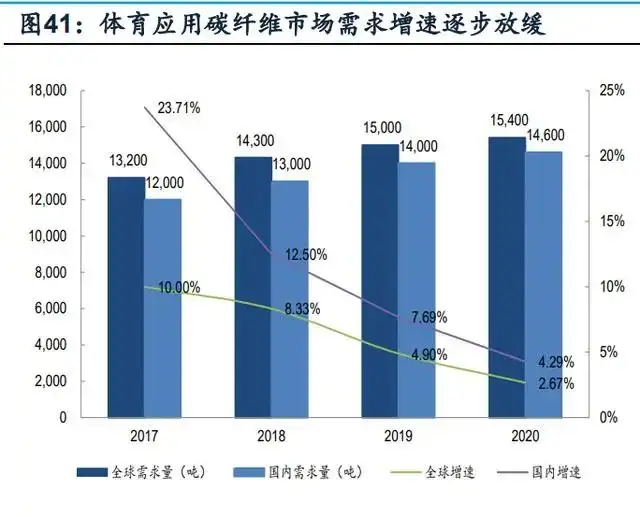
內(nèi)容來源:慧博行業(yè)研究報(bào)告庫(kù)
報(bào)告出品方/作者:廣發(fā)證券,孟祥杰
版權(quán)聲明:復(fù)材云集尊重版權(quán)并感謝每一位作者的辛苦付出與創(chuàng)作;除無法溯源的文章,我們均在文末備注了來源;如文章視頻、圖片、文字涉及版權(quán)問題,請(qǐng)第一時(shí)間聯(lián)系我們,我們將根據(jù)您提供的證明材料確認(rèn)版權(quán)并按國(guó)家標(biāo)準(zhǔn)支付稿酬或立即刪除內(nèi)容!